Wie viel graue Energie steckt im grünen Dämmstoff?
Schon lange vor dem Siegeszug der Mineralwolle- und Styropordämmstoffe nutzte man Holzfaserplatten, um damit Gebäude zu dämmen. Erste Produkte waren schon in den 30er-Jahren des letzten Jahrhunderts auf dem Markt. Man verwendete sie hauptsächlich als Akustikplatten und nutzte sie in Form einer (dünnen) Innendämmung vor allem im Bereich von winddichtenden Unterdeckungen. Beliebt waren diese Platten in bituminierter Ausführung auch als zweite Ebene des Regenschutzes unter Ziegeln und anderen Eindeckungen. Fast komplett vom Markt verdrängt, rückten sie in den 80er-Jahren aufgrund ihrer Diffusionsoffenheit für das ökologische Bauen ohne Dampfbremsfolien wieder in den Fokus von Planern und Handwerkern.
Durch die Entwicklung von regendichten Nut- und Federprofilen in den 80er-Jahren waren sie bald die gefragte Ergänzung für die aufkommenden Zellulose-Einblasdämmungen für die Dachschräge. Als sich in den 90er-Jahren beim handwerklichen Holzrahmenbau das Konzept der innenliegenden Holzwerkstoffplatte als moderat dampfbremsende und luftdichtende Beplankung recht schnell bewährte, waren Holzfaserdämmplatten als Unterfassade die naheliegende Ergänzung auf der Außenseite.
Mit steigenden Anforderungen an den Wärmeschutz entstand der Bedarf, dickere Platten als anfangs üblich (12 bis 22 mm) zu produzieren. Eine besondere Herausforderung stellte nach der Jahrtausendwende die Entwicklung von verputzbaren Holzweichfaserplatten für den Holzbau und als Wärmedämmverbundsysteme dar. Seither haben sich Holzfaserdämmplatten vom Nischenprodukt zu einem genormten Baustoff mit einem breiten Anwendungsspektrum entwickelt, hergestellt von mehreren Anbietern mit Werken in verschiedenen europäischen Ländern.
Nass- oder Trockenverfahren: Was ist ökologischer?
Die traditionelle Methode, nach der über Jahrzehnte Holzfaserdämmplatten ausschließlich hergestellt wurden, ist das sogenannte „Nassverfahren“ (Abb. 1). Hierbei werden Hackschnitzel zerfasert und in heißem Wasser zu einem Holzbrei aufgeschlossen. Auf Langsiebe kontinuierlich aufgebracht, wird mittels Presswalzen und Vakuumsaugern etwa die Hälfte des Wassers entzogen. Der Rest bis zur Auslieferungsfeuchte bedarf des Energieeinsatzes in Umlufttrocknern.
Was diese Platten besonders umweltfreundlich macht, ist zweierlei: Es werden keine chemischen Bindemittel zugesetzt. Für die je nach Anwendung nötige Feuchteschutzimprägnierung verwendet man heute anstatt Bitumen unproblematische Stoffe wie Latex oder Paraffinwachse. Das Verfahren erlaubt allerdings nur die Herstellung von maximal 25mm dicken Platten. Über dieses Maß hinaus bedarf es bei der Herstellung eines weiteren Arbeitsganges – dem Verleimen mehrerer Plattenschichten (streifenförmiger Auftrag von Weißleim).
Die zunehmende Nachfrage nach höheren Dämmdicken führte in den letzten zehn Jahren dazu, dass sich nun das Trockenverfahren am Markt zu etablieren begann. Hierbei können durch Zugabe von Bindemitteln einschichtige Platten oder Filze bis 300mm Dicke hergestellt werden. Bei Plattenware sind dies PU-Leime in nennenswerter Menge, und für Filze verwendet man textile Kunstfasern.
Da drängt sich sogleich die Frage auf: Ist das der blinde Fleck dieser Öko-Produkte? In den Umwelt-Produkt-Deklarationen (EPD) ist dazu leider wenig Konkretes zu finden. Und auch die eigenen Angaben der Hersteller in ihren Produktbeschreibungen enthalten nicht immer klare chemische Bezeichnungen zu den verwendeten Klebern. Vor allem fehlt in vielen Fällen eine nachvollziehbare produktspezifische Prozentzahl zum Anteil der verwendeten Bindemittel – und damit auch zu deren Beitrag bei der grauen Energie.
Zu dieser Verwirrung tragen die EPD selbst bei, wenn dortige Prozentangaben auf einer „produktionsvolumengewichteten Durchschnittsmenge“ basieren, und dieser Durchschnitt sowohl Platten im Nass- als auch im Trockenverfahren enthält. Legt man die von einigen Herstellern angegebenen rund 5 bis 8 Masse-% PUR-Harz zugrunde, enthalten zumindest die Platten mit hoher Rohdichte durchaus 10 bis 15 kg pro m³ an Leimen mit einer hochtoxischen Prozesskette. Das ist zwar nur ein Zehntel im Vergleich zu „reinen“ PU-Dämmplatten, aber auch nicht ganz ohne.
Bindemittel bei Gefachdämmstoffen
Günstiger sieht die Bindemittelfrage bei den Dämmfilzen aus. Die hierbei verwendeten Stützfasern sind in der Regel aus Polyethylen (PE) und Polypropylen (PP), also reine Kohlenwasserstoffe und keine Produkte der Chlorchemie. Sie werden nach der Beimengung in den Holzfaserkuchen durch Erhitzen angeschmolzen und tragen so zur flexiblen Bindung bei.
Zur quantitativen Bedeutung sind die Angaben dürftig und schwanken, wenn überhaupt deklariert, zwischen 3 bis 8%. Demnach enthalten 200 mm Holzfaserdämmfilz 0,3 bis 0,8 kg/m² PE/PP. Das entspricht der Masse einer 0,2 bis 0,5 mm dicken PE-Folie. Eine unbequeme Wahrheit? Leider wird dieses Thema bei den Deklarationen dezent ausgeblendet.
Die mit Sicherheit umweltfreundlichste Form der Dämmung von Holzbaugefachen ist das Einblasverfahren mit Dämmstoffen aus nachwachsenden Rohstoffen. Seit mehr als 30 Jahren werden hierfür Zellulosefasern aus dem Upcycling von Tageszeitungspapier verwendet – der Marktführer in diesem Bereich. Durch die Entwicklung einer leistungsfähigeren und besser regulierbaren Maschinentechnik lassen sich seit geraumer Zeit auch gröbere Holzfasern einblasen.
Beide Rohstoffe – also Zellulosefasern und Holzfasern – benötigen in dieser Anwendung prinzipiell keine chemischen Bindemittel, und die Flammschutzmittel bestehen aus unproblematischen mineralischen Salzen.
Die Primärenergie-Effizienz von Dämmplatten aus Holzfaser
Betrachten wir als erstes den Energieaufwand zur Herstellung von dämmenden Holzfaserplatten. Abb. 2 zeigt einen eindeutigen Zusammenhang der aufzuwendenden „grauen Energie“ und der Rohdichte der Endprodukte. Klar: Je mehr Material aufbereitet werden muss, desto höher der Energieeinsatz.
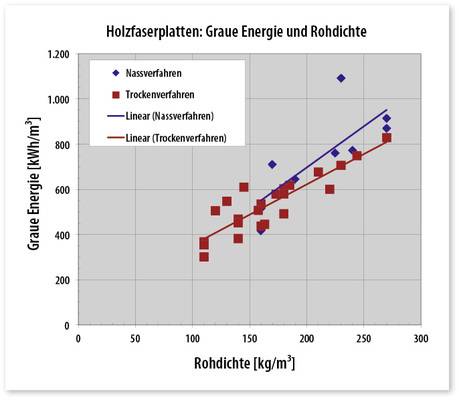
Allerdings ist die Schwankungsbreite bei Produkten mit derart geringer Rohdichte recht groß – auch für den gleichen Verwendungszweck. Dies ist zum einen der unterschiedlichen Energieeffizienz der Herstellerwerke und der Art der verwendeten Energieträger geschuldet. Zum anderen schlägt hierbei zu Buche, dass die EPDs einiger Hersteller nicht produktspezifisch, sondern für eine „gemittelte Rohdichte nach Verkaufszahlen“ deklariert worden sind.
Die linearen Trendlinien zeigen, dass das Nassverfahren – abgesehen davon, dass niedrige Rohdichten nicht möglich sind –, tendenziell einen größeren Energieinput benötigt. Dieser ist im Wesentlichen auf die hohe Produktionsfeuchte zurückzuführen, die eine energieintensive Trocknung erfordert. Dass die Unterschiede bei vergleichbarer Rohdichte im mittleren Bereich dennoch nicht besonders groß sind, weist darauf hin, dass die chemischen Bindemittel im Trockenverfahren eben auch eine nennenswerte Menge an grauer Energie enthalten. In der Regel steht dieser Anteil an der zweiten Stelle des gesamten Energiebedarfs aus der Herstellung.
Im ersten Teil dieser Recherche hatten wir zu Bewertung der Primärenergie-Effizienz auch die -Werte der jeweiligen Dämmstoffe einbezogen. Abb. 3 zeigt dies für die verschiedenen Holzfaserplatten in Abhängigkeit von typischen Rohdichtebereichen und dem Herstellungsverfahren.
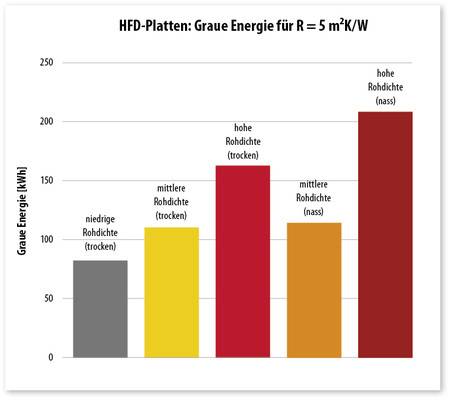
Vergleicht man diese Werte mit konventionellen Dämmstoffen, die ähnliche Eigenschaften und Anwendungsbereiche aufweisen, so liegen Holzfaserplatten niedriger Rohdichte (als Dämmstoff für WDV-Systeme) am unteren Rand der Spannweite der grauen Energie für weißes EPS (85 bis 110 kWh/m²). Gegenüber einem WDVS aus „grauem EPS“ mit = 0,032 W/mK beträgt der Energieeinsatz hingegen nur 58 kWh/m² bei gleichem Dämmwert.
Betrachten wir den Anwendungsbereich druckbelastbarer Holzfaserplatten mittlere Rohdichte, so liegt deren Inhalt an grauer Energie in ähnlicher Größenordnung wie die Hartschaumstoffe (100 bis 130 kWh/m² bei R = 5 m²K/W). Lediglich die Platten mit hoher Rohdichte, ganz besonders wenn sie im Nassverfahren hergestellt werden, fallen bei gleichem U-Wert durch einen deutlich höheren Energieinhalt auf – nicht zuletzt, weil sie nur -Werte von 0,043 bis 0,051 W/mK aufweisen. Da es sich aber hierbei in der Regel um Unterdeckplatten handelt, ist ein Vergleich mit konventionellen Dämmstoffen mangels eines entsprechenden Angebots am Markt, zu dem es EPD gibt, nicht möglich.
Gefachdämmungen aus nachwachsenden Rohstoffen
Der größte Teil des Dämmvolumens befindet sich bei Holzbauteilen im Gefachbereich. Die ersten Faserdämmstoffe aus nachwachsenden Rohstoffen, die in diesem Bereich eine nennenswerte Bedeutung erreichten, waren Zelluloseprodukte. Über die „Zwischennutzung“ als Tageszeitungspapier entstammen sie letzten Endes aus dem nachwachsenden Rohstoff Holz. Diese Form des Upcyclings macht aus dem kurzlebigen Produkt „Zeitungspapier“ einen langlebigen, energiesparenden Baustoff.
Bezüglich des Verbrauchs an Herstellungsenergie hatte seit der Veröffentlichung der ersten Studien [1] dieser Dämmstoff ein Alleinstellungsmerkmal: Mit nur rund 60 kWh/m³ lag die Zellulose bei weniger als der Hälfte der günstigsten Gefachdämmstoffe aus Mineralfasern. Neuere Untersuchungen, die im Zuge von Umwelt-Produktdeklarationen erfolgten, haben dies bestätigt. Bei gleichem R-Wert (5 m²K/W) steht dem Mittelwert bei Zellulose (11,5 kWh/m²) ein fast dreifacher Durchschnitt bei Mineralfaserfilzen (31 kWh/m²) gegenüber.
In jüngerer Zeit sind auch für die Gefachdämmung flexible Matten und Einblasdämmstoffe auf Holzfaserbasis auf dem Vormarsch. Sie werden generell im Trockenverfahren produziert. Da für die Filze allerdings besondere Bindemittel und spezifische Produktionsverfahren erforderlich sind, wären hierzu auch produktbezogene Untersuchungen erforderlich. Die überwiegende Anzahl der Anbieter hielt augenscheinlich solchen Zusatzaufwand bislang nicht für erforderlich.
Zwei spezifische Deklarationen, die ein eigenes EPD für Dämmfilze enthalten, zeigen allerdings Endergebnisse, die um einen Faktor von mehr als zehn (!) auseinander liegen. Das deutet darauf hin, dass bei diesem Produkt wohl auch noch erhebliche methodische Schwierigkeiten seitens der Prüfinstitute existieren.
Also kann gegenwärtig die ganzheitliche Gebäudeplanung (von der Wiege bis zur Nutzungsphase) mit diesen Produkten nichts anfangen. Eigentlich schade, denn Holzfaserprodukte mit geringer Rohdichte und unproblematischen Bindemitteln (oder sogar ganz ohne, wie beim Einblasverfahren) haben durchaus das Potenzial, mit einem sehr niedrigen Niveau an grauer Energie punkten zu können. Hier ist die Initiative der Hersteller und ihrer Verbände gefragt.
Ähnliches gilt auch für die vielen Anbieter von „Naturdämmstoffen“. Alle Hersteller, die Hanf, Flachs, Jute oder andere nachwachsende Rohstoffe verwenden, haben bislang keine EPD erstellen lassen. Einzig der „Exot“, die Strohballenbauweise, kann quantitativ durch eine EPD belegen, dass man mit nur 17 kWh/m³ trotz des mäßigen -Werts (0,052 W/mK) die Primärenergieeffizienz von Zellulose-Einblasdämmungen noch unterbieten kann.
Fazit und Ausblick
Durch die sich häufenden Umweltproduktdeklarationen verbessert sich zunehmend die gesicherte Basis für die Kalkulation von Energiebilanzen, die „graue Energie“ aus der Herstellung der Materialien einbeziehen. Im Detail ergibt sich hieraus auch die Erkenntnis, dass das Überdrehen einer bestimmten Stellschraube im Gesamtsystem – sprich: die Wärmeleitfähigkeit der Dämmstoffe - zu kontraproduktiven Ergebnissen führen kann, insbesondere bei Mineralfaserdämmstoffen. Bei den Schaumkunststoffen bietet das „graue“ EPS die umweltschonendste Optimierung von -Wert und Herstellungsenergie.
Lange galten Holzfaser-Dämmplatten als Außenseiter bei der Primärenergie-Effizienz, bedingt durch den produktionstechnisch hohen Einsatz an Hilfsenergie und auch wegen der schlechten Dämmwerte. Dies hat sich durch Innovationen der Hersteller geändert. Für vergleichbare Zwecke können sie mit konventionellen Dämmstoffen durchaus mithalten. Ihre Entsorgung ist am ehesten geeignet, bei Umbau und Abriss durch eine thermische Verwertung in einem Biomassekraftwerk mit Wärmeauskopplung die eingespeicherte Sonnenenergie zu nutzen.
Unbestritten liegen Holzfaser-Unterdeckplatten mit höherer Rohdichte hinsichtlich der Energieaufwendungen zur Herstellung deutlich höher. Hier haben sie allerdings aus bauphysikalischer Sicht keine wirkliche Konkurrenz, die vergleichbare Wetterschutzeigenschaften mit Diffusionsoffenheit und Dämmwirkung kombinieren könnten.
Als Gefachdämmung bleibt nach wie vor die Einblasdämmung mit Zellulose in der Energiebilanz ungeschlagen – sie punktet also nicht nur als lückenlose Hohlraumdämmung sondern auch durch den mit Abstand niedrigsten Inhalt an „grauer Energie“.
Auch andere Dämmstoffe aus nachwachsenden Rohstoffen haben das Potenzial zu sehr geringem Energieeinsatz in der Produktion. Leider fehlen hierzu bislang die Nachweise über geprüfte Umwelt-Produktdeklarationen – die Hersteller täten gut daran, diesen Beleg endlich zu liefern, um den Kritikern ihre Argumente widerlegen zu können.
Wann rechnet sich bei Holzfaserdämmstoffen ein besserer -Wert?
Als Nebenprodukt zur Recherche der Grauen Energie ist der Autor auf eine ausführliche Preistabelle eines Holzfaserherstellers gestoßen, die es erlaubt, eine häufig gestellte Frage zu analysieren: Lohnt es sich denn finanziell, sich immer für Produkte mit besseren Wärmeleitfähigkeiten zu entscheiden? Die Ergebnisse sind teils wie zu erwarten, teils aber auch überraschend. In der unten stehenden Tabelle werden vier Gruppen der vielfältigen Anwendungsgebiete von Holzfaserdämmungen miteinander verglichen:
- Bei Platten für Wärmedämm-Verbundsysteme ist die Antwort einfach: Besser dämmende Platten mit geringerer Rohdichte sind billiger. Der Wechsel zu Platten, die im Nassverfahren hergestellt werden, weisen gegenüber der Trockenvariante mit 110 kg/m³ einen um 24 % höheren Wärmeverlust auf und sind gleichzeitig 21 % teurer. Also durchgefallen.
- Bei Unterdeckplatten, die im Trockenverfahren (TV) hergestellt werden, liegen die Wärmeleitfähigkeiten um 10 bis 13 % günstiger als bei Platten aus dem Nassverfahren (NV). Da die TV- Platten aber etwa 5 % billiger sind als NV-Platten, dauert es eine gewisse Zeit, bis sich die Mehrkosten für die wärmetechnisch besseren Platten amortisiert haben. Bei 60 mm Dicke sind dies nur 2,5 Jahre, bei 120 mm allerdings schon gut sieben Jahre.
- Bei Standard-Wärmedämmplatten für die Anwendung auf festen Untergründen (alte Außenwände, Holzschalungen oder Holzwerkstoffplatten) können die umweltfreundlicheren traditionellen Platten aus dem Nassverfahren durchaus wirtschaftlich mithalten. Die wärmetechnische Verbesserung durch das Trockenverfahren ist so gering, dass der Mehrpreis dieser Platten sich erst nach 22 Jahren amortisiert.
- Bei flexiblen Gefachdämmungen kann durch eine erhöhte Rohdichte von 50 auf 60 kg/m³ der -Wert von 0,038 auf 0,036 W/mK gesenkt werden. Die Materialkosten steigen allerdings linear um etwa 4 %. Bei einer Dämmdicke von 100 mm lässt sich der Mehrpreis in gut vier Jahren wieder einspielen. Bei größeren Dämmdicken zeigt sich allerdings mal wieder, dass die U-Wert/Dämmdicke-Kurve eine Hyperbel ist, wohingegen der Preis nahezu linear ansteigt. Bei 200 mm dauert es schon 17 Jahre, bis die Gewinnzone beginnt. Steigt die Dämmdicke weiter, kann es sein, dass die Amortisationszeit die technische Lebensdauer überschreitet.
Kurzum: Es lohnt sich, genauer hinzuschauen, um dem Kunden eine wirtschaftlich und ökologisch optimierte Lösung anbieten zu können – je nach Anwendungsbereich. Man bedenke: Bei anderen Herstellern können das Preisgefüge und die Abstufung der - Werte anders aussehen als in unserem Beispiel.
Dieser Beitrag von Robert Borsch-Laaks ist zuerst erschienen in GEB 01/2020. Robert Borsch-Laaks ist nach langjähriger Arbeit als Sachverständiger für Bauphysik und aktiver Teilnehmer in Normenausschüssen und Fachregelkommissionen im (Un-)Ruhestand weiterhin als Fachautor und Dozent tätig.
Literaturverweise
[1] IBO – Österreichisches Institut für Baubiologie und -ökologie und Donau-Universität Krems, Zentrum für Bauen und Umwelt (Hrsg.): Ökologischer Bauteilkatalog, Bewertete gängige Konstruktionen, Wien/New York (Springer-Verlag) 1999