Maridur: Fugenlose XL-Holzoberflächen lassen sich thermisch formen
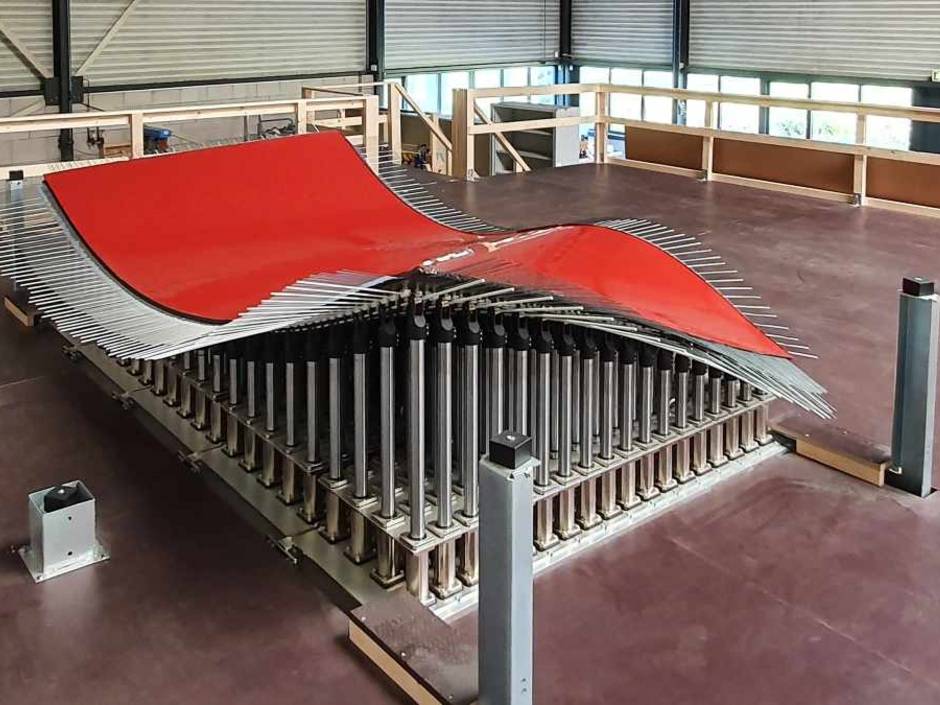
Bereits seit 2008 besitzt Danzer ein Patent für 3D-Furniere aus Holz, mit denen sich komplexe Formen wie Kurven und Radien realisieren lassen. Dazu wird das Furnier im Vorfeld bearbeitet, sodass es sich um das Werkstück legt und nahtlos anpassen lässt. „Um diesen Effekt zu erreichen, schneiden wir das Material in dünne Steifen von 1,2 mm Breite“, erklärt Thomas Wenk, Meister für Holztechnik bei Danzer. „Diese Streifen werden auf der Rückseite mit Klebefäden versehen und dadurch locker zusammengehalten.
Dies spannt ein Raster von etwa 10 mm auf, das leicht nachgibt und sich verformen lässt.“ Auf diese Weise presst Danzer Formteile für beispielsweise Stühle und beschichtet Innenverkleidungen in PKW-Fahrgastzellen sowie Elemente in Yachten und Flugzeugen.
Witterungsbeständiger Werkstoff für Outdoor- und Nassbereiche
Doch gerade im Outdoor- und Nassbereich sind Bauteile aus dem klassischen Werkstoff Holz extremen Witterungseinflüssen ausgesetzt, vor denen sie auch das robuste 3D-Furnier nicht langfristig schützen kann. Bei feuchter Umgebung quellen Holzwerkstoffe etwa schnell auf und bilden über einen längeren Zeitraum Risse. Zudem verfügen sie über keine einheitliche Struktur oder Dichte, weswegen bei der Bearbeitung größere Vorsicht geboten ist, um Schäden an der Oberfläche zu vermeiden. „Im Gegensatz dazu besteht unser Werkstoff Maridur aus homogenem Polyurethan (PU) und ist zu 100 Prozent feuchtigkeitsresistent“, berichtet Stefan Knapp, Anwendungstechniker bei der OBO-Werke GmbH.
In Zusammenarbeit mit Danzer ist es OBO gelungen, Maridur-Platten im Rohzustand thermisch zu verformen und mit einem ebenfalls witterungsbeständigen 3D-Furnier zu beschichten – für Architekten und Designer von Yachten sowie Luxusfahrzeugen ergaben sich damit völlig neue Gestaltungsmöglichkeiten für den Innenausbau wie auch den Außenbereich. Seit Ende 2023 denkt OBO jedoch größer: Der Hersteller holte zusätzlich den niederländischen Formexperten Curve Works mit ins Boot. Dieser verfügt über die technischen Möglichkeiten, auch großformatige Bauteile mittels thermischer Verformung schnell und kostengünstig aus Maridur zu realisieren.
Thermische Verformung und Leichtbau
Für den neuen Kooperationspartner lag die Herausforderung darin, eine qualitativ hochwertige Verarbeitungsmethode für die kürzeste Fertigungszeit zu finden. „Die Wirtschaftlichkeit ist hier nur gegeben, wenn eine große Anzahl an Bauteilen an einem Tag thermisch geformt werden kann“, erklärt Curve Works-Geschäftsführer François Geuskens. Hier spielt die richtige Temperatur eine entscheidende Rolle. Diese liegt bei Maridur bei 120 °C. „Wir hatten den Vorteil, dass unsere Fertigungsinfrastruktur bereits auf die Verarbeitungsbedingungen von Maridur ausgelegt war und wir keine weiteren Anpassungen vornehmen mussten“, so Geuskens weiter. Nach der Erwärmungsphase kann der weiche Werkstoff einfach über die entsprechende Form tiefgezogen oder manuell gedreht werden.
Den großformatigen Bauteilen kommt zudem die Möglichkeit der Sandwichbauweise zugute: In einem Werkstück kann mit verschiedenen Dichten zwischen 80 und 1.600 kg/m3 gearbeitet werden. So lässt sich etwa ein leichter Kern mit einer Oberfläche aus höherer – und damit der jeweiligen Anwendung angemessener, höherwertigerer – Dichte versehen. Im Vergleich zu anderen Werkstoffen, die eine ähnlich hohe Stabilität und Beständigkeit aufweisen, kann auf diese Weise an Gewicht eingespart werden. „Der Leichtbau durch Sandwichbauweise ist besonders bei größeren Deckmöbeln von Yachten oder auch Verkleidungen von anderen Fahrzeugen wie Caravans von Vorteil“, erklärt Knapp. „Denn hier kommt es oftmals auf jedes Gramm an.“
Veredelung freier Formen mit langlebigem Edelholzfurnier
Für die weitere Veredelung wird das Werkstück unabhängig von seiner Größe nach dem Erkalten mit dem patentierten 3D-Furnier von Danzer beschichtet. „Hierfür nutzen wir verschiedene Vakuumtechniken“, berichtet Wenk. „So schmiegt sich das Furnier nahtlos selbst an geschwungene, komplexe und organische Formen an.“ Da sich das Material im Arbeitsfortgang noch bewegen kann, sollte das Bauteil nicht bis zur äußeren Kante beschichtet werden. Sobald die 3D-Edelholzoberfläche verklebt ist, handelt es sich um ein starres Werkstück, welches sich nicht mehr verformen lässt. Allerdings kann es nun bei Bedarf weiter gefräst werden.