So werden Installations- und Sicherheitsvorgaben bei PV-Anlagen eingehalten
Der kräftige PV-Zubau kann angesichts des sich ausweitenden Fachkräftemangels zu mehr Planungs- und Installationsfehlern führen. Umso wichtiger ist es, dass sich Planer:innen und Errichter:innen von Sachverständigen unterstützen lassen, um die passende Lösung auszuwählen und sie ordnungsgemäß in Betrieb zu nehmen. Zudem können die PV-Expert:innen mit einfachen Prüfungen die Effizienz der Anlage sichern. So prüft beispielsweise der TÜV Süd in jedem Stadium die Betriebssicherheit und die Wirtschaftlichkeit von PV-Anlagen und Batteriespeichern.
Photovoltaikanlagen arbeiten wirtschaftlich attraktiv, weil sie selbst angesichts steigender Anschaffungskosten nach wie vor langfristig planbare Renditen versprechen. Diese wirtschaftliche Attraktivität besteht jedoch nur so lange keine Mehrkosten durch Reparaturen oder erforderliche Umbaumaßnahmen entstehen – etwa durch Planungsfehler, Mängel bei der Errichtung der Anlage oder statisch ungeeignete Dachkonstruktionen. Der Teufel steckt im Detail, denn bereits kleine Fehler wie einzelne defekte Zellen, geringe Unschärfen in der Dimensionierung oder unzureichende Betrachtungen von baulichen Details können zu hohen Verlusten führen. Ergo: Investitionen in PV-Anlagen sollten gut abgesichert sein. Je höher die Investition, desto eher.
Ohne Prüfung geht es nicht
Für PV-Anlagen gelten eindeutige Installations- und Sicherheitsvorgaben. Vor der ersten Inbetriebnahme und danach in regelmäßigen Abständen sind Prüfungen erforderlich, die die Einhaltung dieser Vorgaben gewährleisten. Gegenstand dieser Prüfungen sind zum Beispiel die Verschaltung der Module zu Strings, die Anordnung und Funktion der Wechselrichter sowie die Durchgängigkeit aller Leiter und sämtliche Isolationswiderstände. Weitere Prüfungen legen das Augenmerk auf den Brandschutz sowie den Schutz gegen elektrischen Schlag. Funktionsprüfungen von Schutzmaßnahmen sollen im Falle eines Fehlers schlimmere verhindern.
Die Durchführungsanweisung zur Unfallverhütungsvorschrift 3 [1], die DIN VDE 0100-712 [2] und die VDE 0126-23-1 [3], beschreiben Inhalte und Ablauf der durchgeführten Prüfungen. Ein gründlicher Check vor der Inbetriebnahme offenbart neben Mängeln bei Planung und Installation auch Produktionsfehler, etwa defekte Freilaufdioden. Mit einer sachgemäßen Installation sorgen Anlagenbetreiber für den bestmöglichen Ertrag von Betriebsbeginn an. Die wiederkehrenden Prüfungen decken in der Folge Schäden auf, die durch Witterungseinflüsse oder Verschleiß entstehen und den Ertrag mindern oder die Sicherheit gefährden.
Auch für kleinere Anlagen empfiehlt sich eine Prüfung, etwa wenn Garantien der Bestandteile ablaufen oder bevor die Gewährleistungspflicht des Errichters endet. Anhand der Prüfprotokolle lassen sich Defekte im Streitfall objektiv nachweisen und für die Versicherung dokumentieren. Jede Prüfung von PV-Anlagen und Batteriespeichern erfüllt also nicht nur gesetzliche Verpflichtungen, sondern liefert auch wertvolle Erkenntnisse über die Effizienz der Anlage und deckt mögliche Defekte frühzeitig auf.
Die Prüfintervalle werden anlagenspezifisch anhand den in der Unfallverhütungsvorschrift 3 niedergeschriebenen Vorgaben sowie gegebenenfalls vorhandener versicherungsrechtlicher Anforderungen festgelegt. Dabei sollen die betrieblichen Umgebungsbedingungen und Erfahrungswerte von anderen Anlagen einbezogen und damit sichergestellt werden, dass Mängel frühzeitig bemerkt werden. Auch das Alter der Anlage spielt eine Rolle. Prüfintervalle können deshalb zwischen 12 und 48 Monate lang sein und müssen im Rahmen einer Gefährdungsbeurteilung festgelegt werden. In die Dokumentation fließt nicht nur der aktuelle Anlagenzustand zum Prüfzeitpunkt ein, sondern auch Veränderungen über den gesamten Lebenszyklus.
Für die Expert:innen von TÜV Süd liegt ein entscheidender Erfolgsfaktor neben der Durchführung der Prüfungen in ihrer Qualität. Ausbildung und Erfahrung des eingesetzten Prüfpersonals beeinflusst maßgeblich die Qualität der Prüfungen. Nur durch langjährige Erfahrung lässt sich gewährleisten, dass Messwerte korrekt interpretiert, Fehler sicher erkannt und praxisnahe Handlungsempfehlungen zum Weiterbetrieb der Anlage gegeben werden.
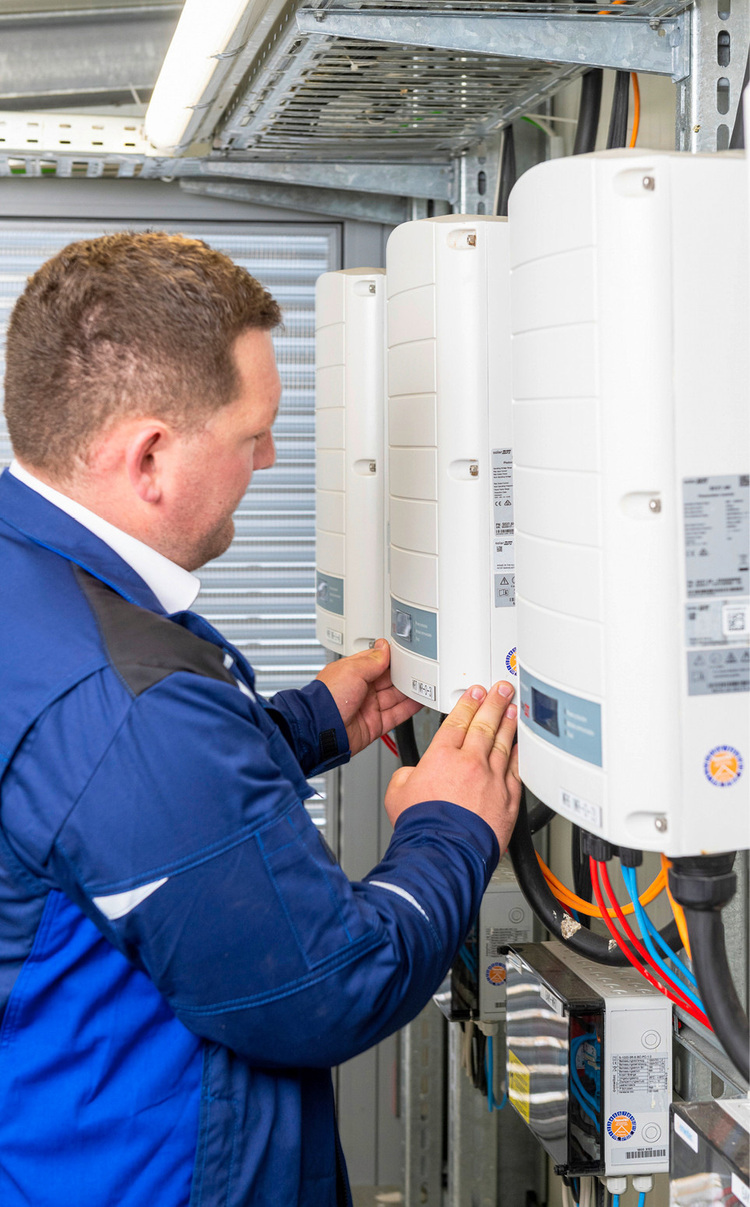
Sicherer als gedacht
Grundsätzlich geht von Photovoltaikanlagen keine höhere Brandgefahr aus als von jeder anderen Elektroinstallation – vorausgesetzt, Planung, Installation und Wartung erfolgen fachgerecht. Das Fraunhofer Institut für Solare Energiesysteme hat in einem Untersuchungszeitraum von 20 Jahren lediglich 120 von PV-Anlagen verursachte Brände in Deutschland erfasst. Lediglich in zehn Fällen brannten die Gebäude ab.
Ein Risiko stellt allerdings die Tatsache dar, dass PV-Anlagen grundsätzlich „angeschaltet“ sind und bei Sonneneinstrahlung immer Spannung führen. Je nach Dimensionierung der Strings und der Intensität der Sonneneinstrahlung betragen die Spannungen bis zu 1.500 Volt DC, welche bei Fehlern potenziell tödlich sein können.
Auch von angeschlossenen Batteriespeichern kann Gefahr ausgehen. Brennende Batteriespeicher sind nur schwer zu löschen und bauen im Falle eines thermischen Durchgehens der Zellen einen hohen Druck auf, der die Wirkung baulicher Brandschutzmaßnahmen außer Kraft setzen kann. Deshalb sind ab einer gewissen Speichergröße spezielle Aufstellräume mit besonderen Schutzmaßnahmen erforderlich. Die Anforderungen sind in der neuen Muster-Verordnung über den Bau- und Betrieb von elektrischen Betriebsräumen [4] geregelt.
Doch nicht nur der vorbeugende Brandschutz ist zu beachten, denn PV-Anlagen stellen auch an die Feuerwehr spezielle Anforderungen. Als Schutzmaßnahme dient beispielsweise ein Feuerwehrschalter, der bei einem Einsatz die Energieführung unterbricht. Als Information für Rettungskräfte im Brandfall müssen Hinweise vorhanden sein; zusätzlich helfen Übersichtspläne, die die Generatoren und den Leitungsverlauf anzeigen.
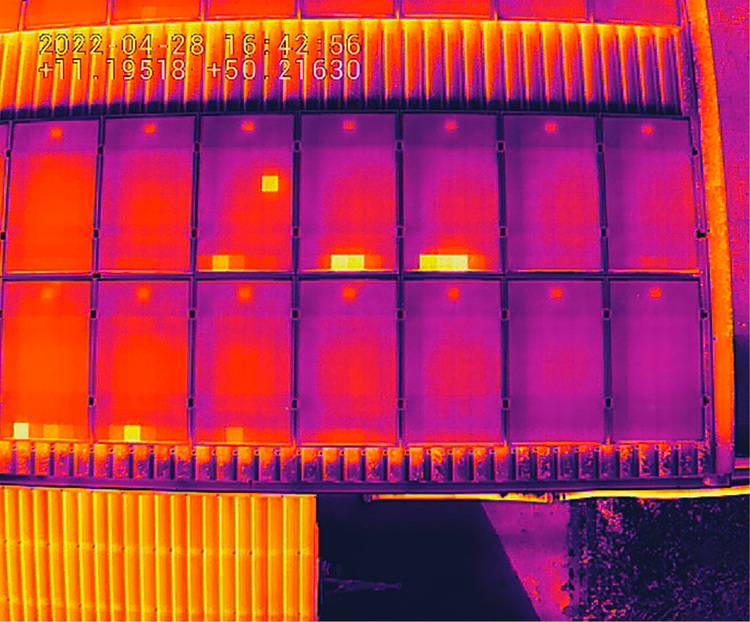
Jeder Fehler kostet
Die Betriebssicherheit einer Anlage beginnt mit der fachgerechten Planung und der korrekten Installation fehlerfreier Bauteile, worin schon zum Teil erheblicher Optimierungsbedarf besteht. So schätzt der Gesamtverband der Deutschen Versicherungswirtschaft, dass Ende 2020 etwa ein Fünftel der zwei Millionen installierten PV-Anlagen nicht korrekt errichtet wurden. Unabhängig vom potenziellen Sicherheitsrisiko kann eine Anlage, die von vornherein nicht erwartungsgemäß arbeitet, nie ihren vollen Wirkungsgrad entfalten und wird aus diesem Grund den kalkulierten Ertrag nicht erbringen können. Mit einer gründlichen Qualitätskontrolle vor Einbau und fachkundigen Prüfungen bei Inbetriebnahme und Wartung lässt sich dieses Risiko größtenteils vermeiden.
In einer typischen mittelgroßen Anlage sind etwa 16 Module in Reihe geschaltet und mit dem Wechselrichter verbunden. Diese Einheit wird als String bezeichnet. Eine einzige defekte Zelle eines Moduls kann den Ertrag des gesamten Strings um vier bis sechs Prozent senken. Risse und schadhafte Lötverbindungen erhöhen den elektrischen Widerstand in der Solarzelle. Der erhöhte Widerstand produziert Wärme, und anhand dieser Wärme werden die Fehler sichtbar. Die defekten Bereiche werden deshalb auch Hot Spots genannt (Abb. 1).
Selbst kleinste Mängel beeinträchtigen die Effizienz und werden daher schnell kostspielig. Bei einem String aus 16 Modulen mit einer Einzelleistung von 350 Watt beträgt die Gesamtleistung 5,6 Kilowatt. Ein Kilowatt installierter PV-Leistung produziert in Deutschland 1.000 bis 1.200 Kilowattstunden Strom. Nimmt man fünf Prozent als durchschnittlichen Wert an, um den ein Modul mit defekten Zellen und ohne funktionierende Freilaufdiode(n) die Leistung des Strings reduziert, bedeutet dies einen Verlust von 280 bis 336 Kilowattstunden. Legt man für die Beispielrechnung bei einem hundertprozentigen Eigenverbrauch einen Strompreis von 40 bis 50 Cent je Kilowattstunde zugrunde, ergibt sich bereits eine Einbuße von zwischen 100 und 130 Euro pro Jahr durch ein einziges defektes Modul.
Bei Abweichungen genau hinschauen
Mit turnusmäßigen Sicherheits- und Brandschutzprüfungen ist es außerdem möglich – und, um Synergieeffekte zu nutzen, auch ratsam –, über einen Soll-Ist-Vergleich die Wirtschaftlichkeit zu überprüfen. Der TÜV Süd bietet diese Kombination an. Für die Prüfung der Leistung gleicht moderne Simulationssoftware die tatsächlich vor Ort gemessene Leistung mit den Herstellerangaben ab. Hierbei wird die Strom-Spannungs-Kennlinie (I-U-Kennlinie) der Module aufgenommen und abgeglichen. Signifikante Abweichungen deuten auf mögliche Mängel hin. Das können einfach zu erkennende und zu behebende Einflüsse wie Verschattung durch Bewuchs oder Verschmutzungen sein oder Defekte an den Geräten selbst. Oberflächliche Schäden fallen schon bei Sichtprüfungen auf, Fehler in den Zellen werden spätestens bei einer tieferen optischen Prüfung erkennbar. Hierfür stehen verschiedene Methoden zur Verfügung.
Weil sich Defekte an PV-Modulen häufig durch Wärmeentwicklung erkennen lassen, bietet sich die Thermografie als Methode an, den Zustand der Anlagen zuverlässig zu erfassen. Schon mit einfachen Wärmebildkameras lassen sich Schäden an der Moduloberfläche sichtbar machen (Abb. 2). Das Verfahren ermöglicht es, konkrete Schäden wie unterbrochene Strings, defekte Zellen oder gänzlich inaktive Module zu identifizieren. Allerdings ist es witterungsabhängig und eignet sich nicht zur Früherkennung von Defekten.
Detaillierter wird es mit der inversen Thermografie. Bei diesem auch als Rückstromthermografie bezeichneten Verfahren werden die PV-Module extern mit Strom – quasi umgekehrt – betrieben. Inaktive Abschnitte oder Anschlüsse mit besonders hohem Widerstand sind deutlich zu erkennen. Das Verfahren bietet mehr Details und weist frühzeitiger auf Mängel hin. Es eignet sich besonders für Dünnschichtmodule.
Bei der Elektro-Lumineszenz-(EL-)Messung handelt es sich um eine Form der Rückstromthermografie, die besonders detaillierte Ergebnisse liefert (Abb. 3). Die bestromten Module senden eine Strahlung im Nah-Infrarotbereich mit einer Wellenlänge von lediglich 1.150 Nanometern aus. Spezielle Kameras mit hoher Auflösung machen die Strahlung und auf diesem Wege selbst kleinste Beschädigungen sichtbar. Die EL-Messung erkennt beschädigte Dioden, Fehler an Kontakten, Mikrorisse und verminderte Leistung durch Licht- und Temperatur-induzierte Degradation (LeTID, engl.: Light and elevated Temperature Induced Degradation Benchmark). Die Technik eignet sich insbesondere zur Eingangskontrolle oder für die Prüfung der Leistungsfähigkeit im laufenden Betrieb. Sind die Verläufe der Modulstränge nicht oder nicht ausreichend dokumentiert, lassen sie sich außerdem mithilfe der EL-Messung exakt nachverfolgen.
Alle thermografischen Verfahren lassen sich einsetzen, ohne die Module ausbauen zu müssen, was für einen unkomplizierten und schnellen Prüfablauf sorgt. Die EL-Messung findet außerdem nachts statt und hat damit nur geringen Einfluss auf den Ertrag der Anlage. Moderne Prüftechnologie vereinfacht die Umsetzung zusätzlich: Die eingesetzten Kameras können mit Drohnen bewegt werden. Der Blick aus der Vogelperspektive auf die Anlage ist ohne die früher benötigten Kräne und Hebebühnen möglich geworden.
Der Autor Stefan Veit leitet das Produkt- und Qualitätsmanagement Elektrotechnik beim TÜV Süd Industrie Service.
Literatur
[1] Deutsche Gesetzliche Unfallversicherung: DGUV Vorschrift 3, Elektrische Anlagen und Betriebsmittel, https://t1p.de/geb240760
2] VDE Verlag: DIN VDE 0100-712, Errichten von Niederspannungsanlagen, Teil 7-712: Anforderungen für Betriebsstätten, Räume und Anlagen besonderer Art – Photovoltaik-(PV)-Stromversorgungssysteme, https://t1p.de/geb240761
[3] VDE Verlag: VDE 0126-23-1, Photovoltaik (PV)-Systeme – Anforderungen an Prüfung, Dokumentation und Instandhaltung, Teil 1: Netzgekoppelte Systeme – Dokumentation, Inbetriebnahmeprüfung und Prüfanforderungen, https://t1p.de/geb240762
[4] Muster einer Verordnung über den Bau von Betriebsräumen für elektrische Anlagen (M-EltBauVO), Stand Januar 2009, zuletzt geändert durch Beschluss der Fachkommission Bauaufsicht vom 22.02.2022, https://t1p.de/geb240763