Stromausbeute maximieren: Neue Trackersysteme für Solarmodule
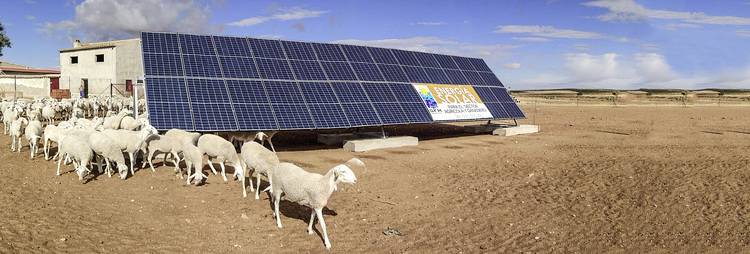
Der Augenblick ist günstig. Bisher haben die Hersteller von Montagegestellen für Solarparks, deren Module dem Lauf der Sonne folgen, eher ein Nischendasein geführt. Inzwischen ist diese Nische größer geworden. Immerhin sind 23 Prozent aller weltweit aufgebauten Solarparks mit solchen sogenannten Trackersystemen ausgerüstet. In diesem Jahr scheint sich die Technologie endlich stärker gegen die fest aufgeständerten Freiflächensysteme durchzusetzen.
Die Prognosen für die Zukunft sind gut. Innovative Lösungen bringen inzwischen solche hohen Erträge, dass sich der Mehraufwand bei der Wartung lohnt. Denn einen Schwachpunkt haben alle Trackersysteme: Sie beinhalten bewegliche Teile, und die sind anfällig für Fehler. Trackersysteme bedürfen deshalb regelmäßiger Pflege. Jedoch ist auch der Energieverbrauch der Trackersysteme gesunken, sodass der Mehrertrag nicht mehr zu einem großen Teil für das Drehen der Systeme aufgewendet werden muss, sondern ins Netz eingespeist werden kann.
Mounting System: Ein Motor für jede Reihe
Die guten Marktprognosen führen dazu, dass auch Hersteller, die bisher einen Bogen um die Trackersysteme gemacht haben, in dieses Segment einsteigen wollen. Einer dieser neuen Marktteilnehmer ist Mounting Systems. Das Unternehmen aus dem brandenburgischen Rangsdorf hat nach einer intensiven Entwicklungsphase in diesem Jahr sein Trackergestell vorgestellt.
Das System basiert auf dem bewährten Sigma, mit dem Mounting Systems schon seit Jahren erfolgreich im Segment der großen und kleinen Solarparks unterwegs ist. Jetzt haben die Entwickler in Rangsdorf dieses Gestell noch beweglicher gemacht. Wie das Sigma I XL Stahl – und wie in der Regel alle Trackergestelle – ist es ein Einpfostensystem. Grundsätzlich stehen für die Gründung des Gestells drei Varianten zur Verfügung. Die häufigste Form ist das Rammen der Pfosten in den Boden. Für steinigen Untergrund haben die Rangsdorfer aber auch Betonfundamente im Portfolio. Für weiche Lehmböden, die zudem periodisch zufrieren und wieder auftauen, kann das System auch mit Schraubfundamenten gegründet werden.
Kniehebelantrieb dreht Modultische
Zusätzlich zu den eigentlichen Pfosten für den Aufbau der Modultische muss noch ein weiterer Pfosten in die Erde gerammt, betoniert oder geschraubt werden, an dem ein Motor befestigt wird. Für jede Gestellreihe mit maximal 130 Metern Länge reicht dabei ein Motor völlig aus. An diesem Motor ist ein Gehäuse befestigt, in dem ein Kettengetriebe untergebracht ist. Über dieses Getriebe wird die Drehbewegung des Motors in eine Längsbewegung gewandelt. Denn für die Nachführung der Module haben sich die Ingenieure von Mounting Systems etwas ganz Besonderes einfallen lassen. Sie drehen die Modultische mittels eines sogenannten Kniehebelantriebs.
Dieser sieht aus wie ein Scherenwagenheber und funktioniert auch so. Er besteht aus vier Schenkeln, die in Rautenform angeordnet sind. Die oberen und unteren Ecken der Rauten werden am Montagepfosten des Gestellsystems und an den Sparren befestigt. Durch die beiden anderen Ecken der Raute schraubt der Monteur eine Torsionsstange, die den Kniehebel bewegt.
Geringer Stromverbrauch für elektrischen Antrieb
Durch die Drehung dieser Stangen mit dem Elektromotor öffnet und schließt sich der Kniehebel. Zunächst ist er maximal in vertikaler Richtung auseinandergedrückt. Um der Sonne zu folgen, dreht der Motor mit einer vorher festgelegten Geschwindigkeit und treibt dabei das Antriebsritzel im Kettengetriebe an. Über die Kette wird die Kraft auf ein größeres Antriebsrad übertragen. In der Mitte dieses Antriebsrades befindet sich eine Welle, an der wiederum die Torsionsstange angebracht ist, auf die die gesamte Drehkraft übertragen wird.
Die Torsionsstange zieht den Kniehebel horizontal zusammen. Dabei werden die Modultische in Richtung Westen gedreht, um der Sonne zu folgen. Ist die Sonne untergegangen, dreht der Elektromotor in die entgegengesetzte Richtung und drückt den Kniehebel wieder auseinander. Dabei werden die Modultische wieder nach Süden in die Ausgangslage gedreht.
An jeden Montagepfosten wird jeweils ein Kniehebelantrieb montiert. Mit dem System nutzt Mounting Systems die Vorteile des Kniehebelantriebs voll aus. Denn mit ihm kann man mit geringem Energieaufwand eine sehr hohe Kraft übertragen. So reicht ein kleiner Elektromotor aus, um die Modultische der gesamten Gestellreihe zu drehen. Der Effekt ist ein sehr geringer Stromverbrauch für den elektrischen Antrieb. Die Rangsdorfer geben diesen mit 1.550 Kilowattstunden pro Megawatt Modulleistung an.
Energieverbrauch gering gehalten
Bei einem zu erwartenden Mehrertrag von 25 Prozent ist dies vor allem in sonnenreichen Regionen leicht zu verkraften. Selbst in Regionen außerhalb des Sonnengürtels der Erde liegt der Strombedarf für die Nachführung der Module damit weit unter einem Prozent dieses Mehrertrags, den die Paneele liefern, wenn sie ständig optimal zur Sonne ausgerichtet sind.
Mit dem neuen System setzt Mounting Systems auf die Vorteile einer unabhängigen Nachführung der einzelnen Gestellreihen. Anders als die Lösungen, die über eine Schubstange oder eine Welle gleich mehrere Reihen mit einem Motor dem Lauf der Sonne nachführen, kann die reihenunabhängige Nachführung auch in hügeligem Gelände eingesetzt werden.
Während der im vergangenen Jahr vorgestellte Tracker von Schletter nur Höhenunterschiede von drei Prozent toleriert, kann der Tracker von Mounting Systems grundsätzlich komplett ohne Einschränkungen bezüglich der Höhenunterschiede zumindest in Ost-West-Richtung installiert werden. Allerdings müssen die Planer von Solarstromanlagen mit solchen Systemen die Verschattung im hügeligen Gelände beachten.
Tracker-Reihen können separat gedreht werden
Ein weiterer Vorteil der unabhängig voneinander nachgeführten Gestellreihen ist die leichtere Wartung. Denn wenn die Tracker mit einer Schubstange oder einer Welle verbunden werden, sind die Räume zwischen den einzelnen Reihen nicht mehr komplett befahrbar. Das erhöht den Aufwand beispielsweise beim Rasenmähen oder beim Reinigen der Module. Auf der anderen Seite ist ein großer, zentraler Motor einfacher zu warten als viele kleine Motoren in den einzelnen Gestellreihen.
Doch die reihenunabhängigen Tracker haben noch einen weiteren entscheidenden Vorteil. Jede einzelne Reihe kann komplett separat zur Sonne ausgerichtet werden, während die Neigung von zentral gesteuerten Systemen nur insgesamt geändert werden kann. Damit werden mit solchen Systemen, wie es Mounting Systems jetzt vorgestellt hat, noch höhere Mehrerträge möglich.
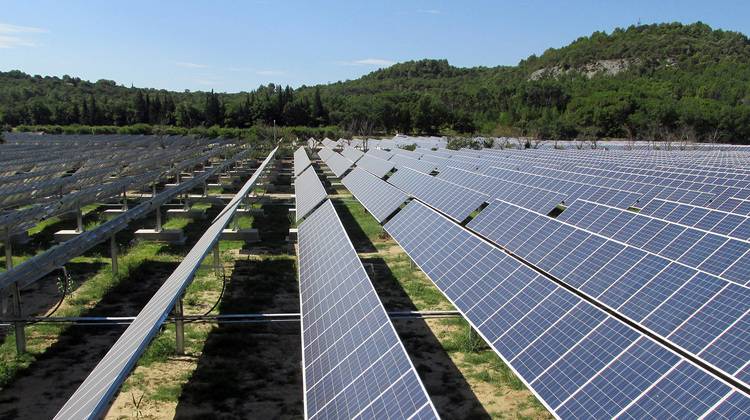
Glaspyramide mit Sensoren
Doch an dieser Stelle gehen die Rangsdorfer den Weg nicht konsequent bis zum Ende. Denn die Nachführung basiert auf einer astronomischen Steuerung. Dabei wird entsprechend dem Standort der Anlage eine konkrete Geschwindigkeit vorgegeben, wie schnell der Tracker dem Lauf der Sonne folgt. Die Steuerung wird so eingestellt, dass sie die jahreszeitlichen Schwankungen von Sonnenauf- und Sonnenuntergang sowie der sich dabei ändernden Sonnenbahn mitberücksichtigt. Allerdings kann die Steuerung nicht auf die tägliche Änderung der Bewölkung reagieren.
Eine große Rolle bei der Entscheidung zwischen astronomischer Steuerung und der Nachführung auf der Basis von aktuellen Daten aus Sensoren spielt die Abwägung zwischen Aufwand und Nutzen. Denn die sensorgesteuerte Nachführung ist zwar effektiver, was den Ertrag betrifft. Sie ist aber auch aufwendiger, wartungsintensiver und störanfälliger als die astronomische Steuerung. Bei dieser können keine Einstrahlungssensoren ausfallen. Sie muss auch nicht gewartet werden. Die sensorgesteuerten Systeme sind hingegen auch in wolkrenreicheren Regionen der Erde besser einsetzbar.
Deger setzt auf Systeme mit Schneckenantrieb
Das neue System, das S100 PF, das Deger Energie aus Horb am Neckar jüngst auf den Markt gebracht hat, besitzt eine solche sensorgesteuerte Nachführung. Dazu hat Deger den MLD-Sensor entwickelt. MLD steht für Maximum Light Detection. Der Sensor sucht ständig nach der maximalen Lichteinstrahlung. Er besteht aus zwei Sensorzellen und einem Logikbaustein, der das Herz des kleinen Geräts ist. Alles ist in einer Glaspyramide untergebracht, sodass die Sensoren auch Licht aus unterschiedlichen Richtungen messen.
Mehrertrag von bis zu 30 Prozent
Auf diese Weise kann der Tracker so gesteuert werden, dass er nicht nur das direkte Sonnenlicht einfängt, sondern auch Licht, das an Wolkenkanten gebrochen und von Schnee, Wasser oder einem hellen Untergrund reflektiert wird. Entscheidend ist dabei, dass die einzelnen Reihen nur in eine neue Position gedreht werden, wenn der zu erwartende Mehrertrag weit über dem Energieaufwand zur Bewegung der Modultische liegt. Mit dieser Steuerung erreicht der Anlagenbetreiber einen Mehrertrag von bis zu 30 Prozent, muss aber dafür in die Sensorpyramide investieren. Damit ist das System jedoch besser für Regionen geeignet, in denen nicht den ganzen Tag über gleichmäßig die Sonne scheint.
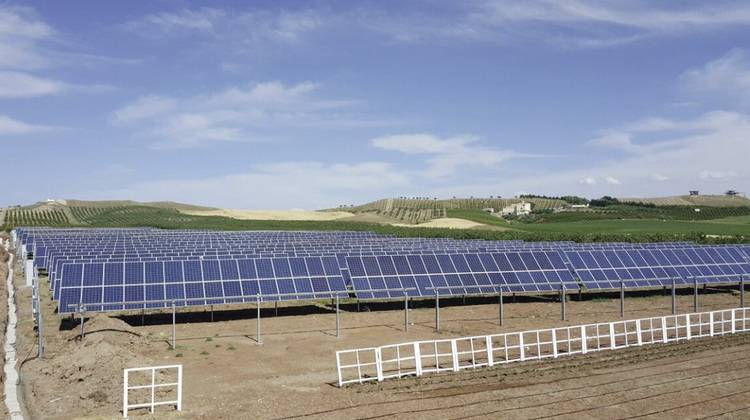
Schneckeantrieb braucht weniger Energie
Der neue Tracker ergänzt das Sortiment um ein Gestell, das mehr Module tragen kann als die bisherigen einachsigen Nachführsysteme. Immerhin passen auf das neue System 44 Standardpaneele mit 60 Zellen, während bei den kleineren Gestellen von Deger bei 26 beziehungsweise 30 Modulen das Maximum erreicht war. Das schafft der Hersteller, indem er die Breite eines Trackers von 15,8 auf gut 23 Meter erhöht hat.
Um die damit im Vergleich zu den bisherigen Systemen größere Last weiterhin mit einem Motor bewegen zu können, hat Deger das neue System mit einem Schneckenantrieb versehen. Die bisherigen einachsigen Tracker wurden mit einem Spindelantrieb bewegt. Der Elektromotor dreht dabei eine Welle, an deren oberem Ende die Schnecke angebracht ist, senkrecht zur Rotationsachse der Module. Diese senkrechte Bewegung wird dann über das Schneckenrad in die horizontale Drehbewegung übersetzt, sodass die Module dem Sonnenlauf folgen können.
Mit diesem neuen Konzept senkt Deger den Energieverbrauch des Trackers. Trotz der höheren Last, die der Motor bewegen muss, braucht er pro Trackereinheit nur noch fünf Kilowattstunden pro Jahr. Die Vorgängermodelle mussten immerhin mit der dreifachen Menge an Energie gefüttert werden.
Jede Trackereinheit steht auf fünf Montagepfosten. Im mittleren dieser Pfosten sind der Motor und der Antrieb integriert. Die maximale Höhe der Modulreihen beträgt – wie bei den vorherigen Systemen – gut 3,40 Meter. Damit passen genau zwei Modulreihen auf den Tracker. Links und rechts können jeweils elf Module nebeneinander installiert werden. Mit diesem Aufbau bringt Deger die höhere Leistung auf den Tracker, bleibt aber trotzdem flexibel. Denn die Tracker können komplett getrennt voneinander aufgebaut werden. Damit sind auch kleinere Systeme für Offgrid-Anwendungen oder die Installation in hügeligem Terrain möglich.
GP Joule setzt auf Gleichstrom-Linearmotor
GP Joule aus Reußenköge in Nordfriesland hat ein eigenes Trackersystem auf den Markt gebracht. Dieses wird über einen selbst entwickelten Algorithmus auf der Basis von sekundengenau eingespeisten Wetterdaten gesteuert. Über diese Steuerung stellt sich das System in 40 gleichmäßig über den Tag verteilten Positionen nach dem an diesem Tag errechneten optimalen Sonnenverlauf ein. Damit ist der Tracker der Nordfriesen ebenfalls für Regionen gut geeignet, in denen das Wetter unbeständiger ist als in den Wüsten Nordafrikas, des Nahen Ostens, Amerikas oder Südeuropas.
Die Modultische werden mittels eines Gleichstrom-Linearmotors – eines sogenannten Linearaktuators – gedreht. Die Linearmotoren funktionieren grundsätzlich nach einem ähnlichen Prinzip wie rotierende Motoren. Der entscheidende Unterschied ist, dass nicht eine Welle gedreht wird, sondern eine Stange – der Läufer – aus dem Gehäuse gedrückt beziehungsweise in dieses hineingezogen wird. In der Vorwärtsbewegung schiebt der Läufer eine Seite der Modultische nach oben, während ein zweiter Linearmotor auf der anderen Seite sich im Rückwärtsgang befindet und den gleichen Modultisch nach unten zieht.
Der Vorteil dieser Motoren ist, dass sämtliche rotierenden Teile, die eventuell gewartet werden müssen, komplett wegfallen. Außerdem benötigt das System keinerlei Getriebe, um eine vertikale in eine horizontale Drehbewegung zu übersetzen. Hier reicht ein einfaches Gelenk, um die lineare Bewegung des Läufers in eine Rotationsbewegung umzuwandeln. Auf diese Weise reduzieren die Nordfriesen die Reibungsverluste, was viel Energie beim Drehen der Modultische spart.
Jeweils ein paar der Linearmotoren können Module mit einer Gesamtleistung zwischen 17 und 27 Kilowatt bewegen. Das ist abhängig von der Leistung der einzelnen Module. Der Tracker ist in Segmenten von jeweils zwölf Modulen aufgebaut. Jedes Segment steht dabei auf jeweils zwei Pfosten, wobei sich zwei benachbarte Segmente einen Pfosten teilen.
Systeme müssen sich auf dem Weltmarkt behaupten
Ob die drei deutschen Hersteller mit ihren neuen Systemen auf dem Weltmarkt punkten können, wird sich noch zeigen. Immerhin realisiert Deger nur wenige Wochen nach der Einführung des S 100 in den Markt den ersten Solarpark mit einer Leistung von 1,75 Megawatt. In der südosttürkischen Provinz Hatay werden im kommenden Frühjahr 150 der neuen Tracker stehen und 6.600 Module dem Lauf der üppig scheinenden Sonne nachführen.