So wird die Korrosion bei Wärmeübertragern verhindert
Allein die Tatsache, dass kein Gebrauchsmetall in der Natur in nennenswerten Mengen in reiner Form vorkommt, zeigt, dass an sich korrosionsbeständige Metalle wie Kupfer oder auch Aluminium auf Dauer durch Umwelteinflüsse angegriffen werden, also korrodieren. Vereinfacht gesagt laufen bei dieser Form der Korrosion die chemischen Reaktionen des Herstellungsprozesses „rückwärts“ ab und so werden die Metalle und Legierungen wieder in die Erze überführt, aus denen sie ursprünglich einmal gewonnen wurden, z. B. Aluminiumoxid oder Kupfersulfid.
Sicher, dieser Prozess schreitet in der Regel äußerst langsam und kaum merklich voran – was sich insbesondere bei Kupferdächern und Aluminiumfassaden bemerkbar macht, aber gerade bei Luftkühlern kann sich bedingt durch die Einsatzbedingungen und aufgrund falscher Materialwahl die Korrosion so stark beschleunigen, dass sich innerhalb kürzester Zeit Leistungsverluste oder sogar Leckagen zeigen.
Dazu ein kurzer Blick in die Chemie: Auf mikroskopischer Ebene ist die Oberfläche eines Metalls nicht statisch, sondern ständiger Veränderung unterworfen. Während die Atome im Inneren von allen Seiten von anderen Metall-Atomen umgeben sind und so ihre Elektronen vollständig absättigen können, fehlen den Atomen an der Oberfläche teilweise die dafür nötigen Partner.
Sie behelfen sich aber, indem sie Moleküle aus der Umgebung an die Festkörper-Oberfläche binden. Teilweise gehen die Oberflächenatome dabei neue Bindungen mit diesen Molekülen ein und geben damit ihren metallischen Charakter auf. Dies führt bei sämtlichen Gebrauchsmetallen dazu, dass sich an Luft oder auch unter Wasser innerhalb kürzester Zeit auf der blanken Metalloberfläche eine dünne unmetallische Schicht aufbaut.
Ob es sich dabei bereits um die ersten Stufen eines korrosiven Angriffs handelt, hängt von vielen Faktoren ab. Je nach Art des Metalls und der Umgebung kann diese Schicht nämlich die weitere Korrosion stark verlangsamen (bspw. Aluminium) oder aber auch kaum merklichen Einfluss auf die Geschwindigkeit der an der Metalloberfläche ablaufenden chemischen Reaktionen haben (bspw. unlegierter Stahl).
Korrosion ist nicht gleich Korrosion
Bei Wärmeübertragern spielen von den in der DIN EN ISO 8044 beschriebenen 56 Formen von Korrosion vorrangig fünf Ausprägungsformen eine Rolle (Bilder):
- Gleichmäßige Flächenkorrosion
- Lochkorrosion (Lochfraß)
- Muldenkorrosion
- Spaltkorrosion
- Kontaktkorrosion (= Bimetallkorrosion oder galvanische Korrosion)
Die genannten Korrosionsarten lassen sich alle auf das gleiche Grundprinzip, nämlich auf den Mechanismus der elektrochemischen Korrosion, zurückführen. An der Oberfläche eines Metalls laufen dabei stets zwei Teilreaktionen ab. Zum einen gibt das Metall im Bereich der Anode Elektronen ab, welche durch andere Reaktionspartner im Bereich der Kathode aufgenommen werden. Meist ist dieser Reaktionspartner Sauerstoff.
O2 + 4e- + 2H2O 4 OH-
Wasser kommt in diesem Prozess eine besondere Rolle zu, da es Salze lösen und Ionen leiten kann und damit als Elektrolyt dient (Bild 1).
Wasser ist rund um einen Wärmeübertrager immer vorhanden, sei es als Kondensat, Regen oder Luftfeuchtigkeit. Je länger und je häufiger Feuchtigkeit auf eine Oberfläche einwirkt, desto schneller laufen Korrosionsvorgänge ab. Ähnliches gilt für die Temperatur. Je höher diese ist, desto schneller schreitet die Korrosion voran. Das bedeutet, dass Luftkühler in Normal- und Pluskühlräumen stärker vor Korrosionsangriffen geschützt werden müssen, als es für vergleichbare Geräte im Tiefkühlbereich nötig ist.
Ob ein metallisches Werkstück korrodiert oder eine Schutzschicht ausbildet, hängt letztlich davon ab, was mit den Metallatomen geschieht, welche Elektronen abgegeben haben. Nur ein Teil dieser positiv geladenen Metall-Ionen löst sich im Wasser. Der Rest reagiert mit in Elektrolyten vorhandenen, negativ geladenen Ionen zu Metallsalzen und bildet im Bereich der Anode Deckschichten aus. Haften diese nur lose und sind eher poröser Natur, können Sauerstoff und Wasser weiterhin fast ungehindert auf das Metall einwirken und dieses zunehmend auflösen.
Beispiele hierfür sind die typischen rostbraunen Stellen, die sich auf Bauteilen aus unlegiertem Stahl bilden und teilweise sogar von selbst abblättern, oder aber auch Grünspan, der beim Einwirken von Essigsäure auf Kupfer entsteht und in nicht unerheblichem Maße in Wasser löslich ist.
Ist die Deckschicht dagegen fest anhaftend und so dicht, dass der Elektrolyt kaum durch sie hindurch bis zur Metalloberfläche vordringen kann, verlangsamen sich die weiteren Korrosionsprozesse deutlich.
Eine sehr bekannte Form einer solchen schützenden Deckschicht ist die Kupferpatina, die aus basischen Kupfersalzen besteht, welche – im Gegensatz zum Grünspan – kaum in Wasser löslich sind (Bild 2).
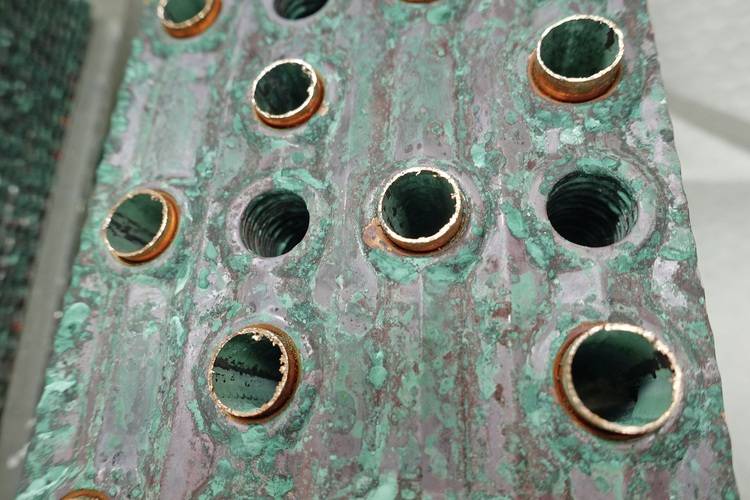
Was ist eine Passivschicht?
In ihrer funktionsweise der Kupferpatina sehr ähnlich, aber um Größenordnungen dünner, sind die sogenannten Passivschichten, die sich beispielsweise auf blankem Aluminium und chromhaltigem Edelstahl (umgangssprachlich oft als rostfreier Stahl bezeichnet) innerhalb kürzester Zeit ausbilden.
Diese – teilweise nur wenige Nanometer dicke – Oxidschicht stellt ebenfalls einen äußerst wirksamen Korrosionsschutz dar. Allerdings sind generell zwei Einschränkungen zu beachten. Zum einen sind die Oxidschichten nicht in allen pH-Wertbereichen stabil, weshalb beispielsweise für Aluminium allgemein nur ein Einsatz bei pH-Werten zwischen 4,5 und 8,5 empfohlen wird.
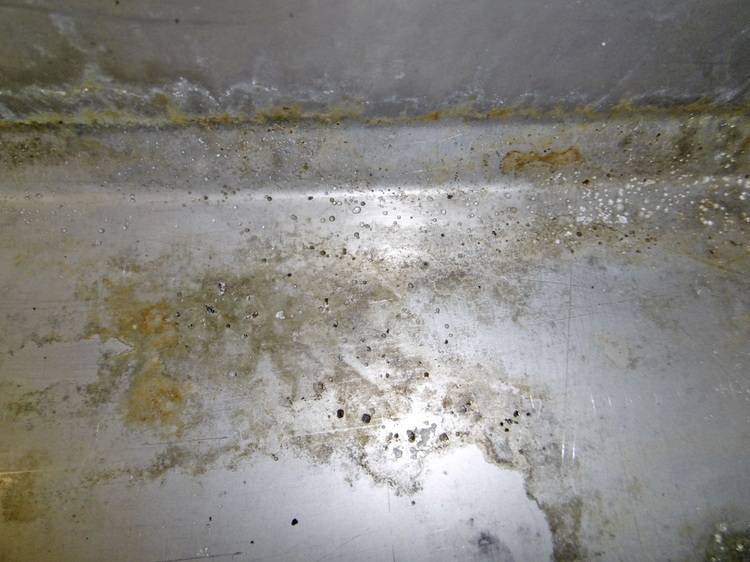
Zum anderen stellt die Oxidschicht genau wie die Metalloberfläche eine sehr aktive Grenzschicht dar, die sich ständig verändert und versucht, alle möglichen Ionen, die sich im Elektrolyten befinden, einzubauen. Gelangen auf diese Art insbesondere Chloride in die Oxidschicht, wird auch diese mit der Zeit undicht und das darunterliegende, reine Metall beginnt sich aufzulösen.
Das Ionengitter wird dabei meist lokal an einzelnen Stellen aufgebrochen. Dieses Phänomen macht sich dann in fortgeschrittenem Stadium als Lochkorrosion bemerkbar (Bild 3).
Die lokale Konzentration einzelner Spezies hat einen sehr großen Einfluss auf die Geschwindigkeit des Korrosionsprozesses. In Spalten, Winkeln und unter anhaftenden Verschmutzungen können sich die Konzentrationen von einzelnen Stoffen deutlich von den Konzentrationen im restlichen Elektrolyten unterscheiden.
Dadurch kann sich an diesen Stellen eine ganz andere Leitfähigkeit und ein stark unterschiedlicher pH-Wert ausprägen. Lokal entsteht dann ein korrosives Milieu, obwohl die eigentliche Zusammensetzung des Elektrolyten keineswegs als korrosiv zu bewerten ist.
So kommt es zu Kontaktkorrosion
Berühren sich zwei Metalle in einem Werkstück (z. B. die Aluminium-Lamelle das Kupferrohr), so definieren sich Anode und Kathode bereits allein durch die jeweiligen elektrochemischen Potenziale der beiden Metalle. Kupfer hat bspw. bei pH 7,5 (neutraler Bereich) ein Potenzial von +0,1 V und Aluminium liegt bei etwa 0,7 V. Kupfer fungiert in dieser Konstellation als Kathode und das unedlere Aluminium als Anode.
Hat die Kathode (zu der die Elektronen wandern) darüber hinaus eine besonders große Oberfläche, gibt die Anode bevorzugt Elektronen ab und der Metallabtrag (die Korrosion) im Bereich der Anode ist entsprechend hoch. Das Flächenverhältnis von Kathode zu Anode ist daher ein maßgeblicher Faktor für die Korrosionsgeschwindigkeit (Bild 4).
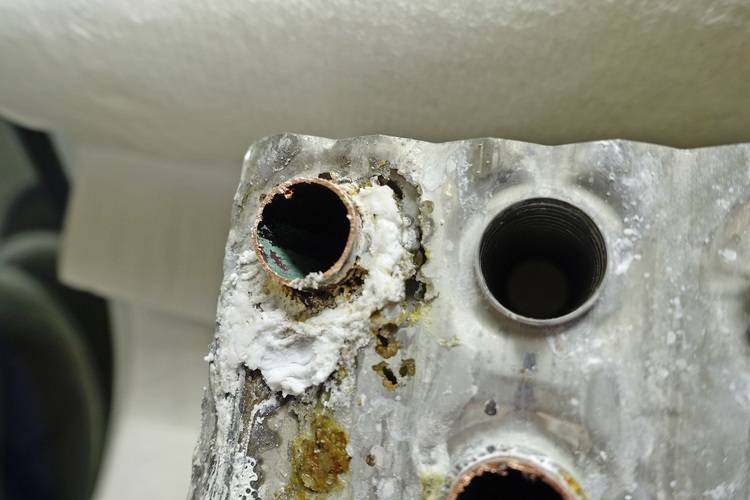
Schädliche Umgebungsbedingungen
Wie eingangs erwähnt, ist jedes Gebrauchsmetall umweltbedingten Veränderungen unterworfen. Wie schnell diese ablaufen, wird maßgeblich von den Umgebungsparametern bestimmt, also Temperatur, Feuchtigkeit, einwirkende Chemikalien usw.
Insbesondere das Halbedelmetall Kupfer wird in Gegenwart von Sulfaten, Acetaten, Chloriden, Ammoniak, Aminen, Stickoxiden, Natronlauge, Hypochloriten, Formiaten etc. so „unedel“, dass es bei zusätzlicher Anwesenheit von Sauerstoff korrodiert und sich auflöst.
Besondere Vorsicht für Wärmeübertrager ist daher geboten, wenn nach einem geeigneten Werkstoff für Anwendungen mit Rauch- und Essigwaren, Fisch, Käse, Abwasser, Gärprozessen und aggressiven Reinigern gesucht wird.
Aluminium verträgt – wie bereits weiter oben erwähnt – weder hohe noch niedrige pH-Werte und die Anwesenheit größerer Mengen an Chloriden ebenfalls nicht. Damit ist es grundsätzlich ohne besonderen Korrosionsschutz für den Einsatz in Räumen, in denen saure Lebensmittel (Dressings, Früchte) und Fisch verarbeitet werden, ungeeignet, und auch maritimes Klima wirkt sich nachteilig auf die Lebensdauer aus.
Außerdem sollte Aluminium weder mit stark basischen noch stark sauren Reinigern in Kontakt kommen.
Die hohe Korrosionsbeständigkeit von rostfreiem Chrom-Nickel-Stahl basiert in erster Linie auf der Bildung einer Passivschicht aus Chromoxid, die selbst gegenüber konzentrierten Laugen und Säuren sehr beständig ist.
Allerdings stören höhere Konzentrationen an Halogeniden wie Fluor, Chlor- und Brom-Ionen die Bildung dieser Passivschicht und machen selbst diese Stähle anfällig für lokale Korrosionserscheinungen, wie Loch- oder Spaltkorrosion. Solch hohe Konzentrationen können beispielsweise bei Verwendung von Chlorid-haltigen Reinigern (Hypochlorit, Aktivchlor etc.) sehr schnell erreicht werden.
Daher müssen selbst Edelstahlkühler nach der Reinigung mit ausreichend Frischwasser nachgespült werden, da sich sonst mit der Zeit Chlorid in Spalten und anderen schwer zugänglichen Stellen lokal anreichert und schnell die kritische Konzentration überschritten ist, ab der Korrosionsprozesse ablaufen.
Maßnahmen zum Korrosionsschutz
Ungünstige Umgebungsbedingungen, die eine Verwendung von Standard-Luftkühlern mit Kupferrohren, Aluminiumlamellen und Gehäusen aus verzinktem Stahl korrosionsbedingt ausschließen, erfordern entsprechende Schutzmaßnahmen. Möglichkeiten sind beispielsweise:
- Erhöhung der Materialstärken
- Verwendung korrosionsbeständiger Materialien (AlMg oder Edelstahl) oder Materialkombinationen (Kupferrohr mit Kupferlamelle)
- Beschichtung einzelner Komponenten bzw. des gesamten Wärmeübertragers
Güntner hat im eigenen Forschungs- und Entwicklungslabor umfangreiche Testreihen durchgeführt, um die Beständigkeit unterschiedlicher Materialien und Materialkombinationen zu testen.
Auf diese Weise – und durch die jahrzehntelange Praxiserfahrung – werden die Produkte ständig iterativ verbessert. Es zeigt sich, dass eine Verdopplung der Materialstärken zwar überproportional die Lebensdauer verlängert, aber sich natürlich auch entsprechend auf den Preis und das Gewicht auswirkt.
Wird statt Kupfer Edelstahl für das Kernrohr eingesetzt, verbessert sich automatisch auch die Korrosionsbeständigkeit und die Lebensdauer kann sich im Vergleich zu einem Standardgerät mehr als verdreifachen.
Allerdings geht diese Lösung mit einem ebenso deutlichen Anstieg des Preises einher. Nicht zuletzt aufgrund der Tatsache, dass für die gleiche Leistung etwa 40 Prozent mehr Fläche benötigt werden.
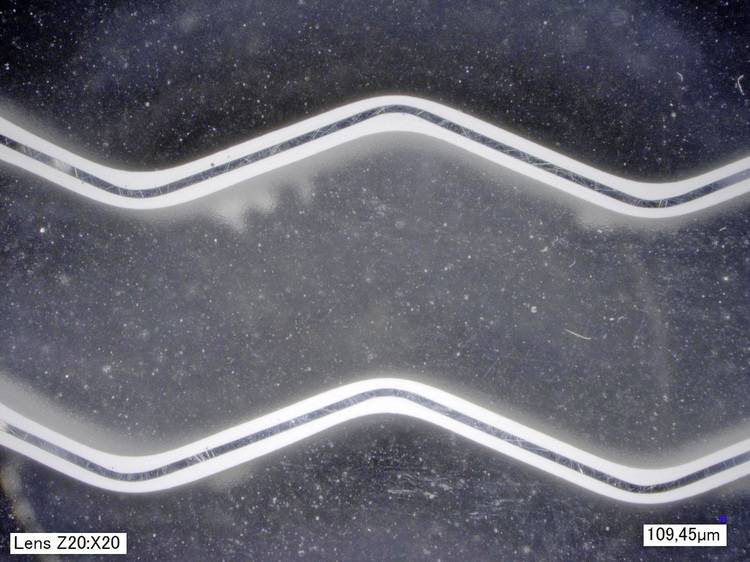
Individuelle Lösungen
Es gibt ähnlich viele Ansatzmöglichkeiten, der Korrosion wirksam zu begegnen, wie es korrosionsfördernde Faktoren im Bereich der Lebensmittelverarbeitung gibt.
Dies ist zum einen auf die unterschiedlichen Lebensmittel zurückzuführen, die gelagert bzw. verarbeitet werden (z. B. Seefisch, Fleisch, Käse, Obst, Essig, Pökelsalz), und zum anderen den dort eingesetzten Reinigern geschuldet, die häufig aggressive, stark saure bzw. alkalische Inhaltsstoffen aufweisen.
Weiterhin haben auch die vorherrschende Luftfeuchte und die Raumtemperatur maßgeblichen Einfluss auf korrosive Prozesse.
Somit ist zwar bei der Suche nach einem langlebigen Luftkühler eine hohe Produktqualität unverzichtbar, aber eine auf den Betreiber individuell zugeschnittene Lösung ergibt sich nur im konstruktiven Dialog der beteiligten Partner.
Daher sind die Anforderungen an ein Gerät insgesamt von der Branche, dem konkreten Anwendungsfall und dem Anwender abhängig.
Weitere Informationen zum Thema sind in der Broschüre „Materialempfehlungen“ von Güntner und in der entsprechenden Güntner App zu finden, welche von der Güntner Homepage heruntergeladen werden können.
Dieser Artikel von Andreas Zürner ist zuerst erschienen in KK - Die Kälte + Klimatechnik Ausgabe: 05-2018.
Güntner Coil Defender
Im Falle von Korrosionsschutz durch Beschichtungen werden bei Güntner zum einen die einzelnen Gehäuseteile der Luftkühler pulverbeschichtet und zum anderen vorbeschichtete Aluminiumbänder zur Produktion Epoxidharz-beschichteter Lamellen verwendet.
In Anlehnung an die DIN EN ISO 12944 erfüllt die Pulverbeschichtung – je nach Schichtstärke – sogar die Anforderungen der höchsten Korrosionsschutzkategorien C5 M lang und C5 I lang.
Und auch die nur wenige Mikrometer dicke Lackschicht der Epoxidharz-beschichteten Lamellen übersteht problemlos 500 Stunden in einer standardisierten Korrosionsprüfung, dem neutralen Salzsprühtest nach DIN EN ISO 9227.
Der Güntner Coil Defender ist ebenfalls eine Pulverlackbeschichtung, die nachträglich aufgebracht wird und sowohl Kernrohre wie auch Lamellen und Stirnbleche im Durchschnitt mit einer 200 µm (0,2 mm) starken Schutzschicht umhüllt.
Mit dieser hochwertigen Beschichtung ist es möglich, dem Kupfer-Aluminium-Wärmeübertragerblock eines Standardluftkühlers eine ähnlich gute Korrosionsbeständigkeit zu verleihen, wie sie vergleichbare Geräte mit Edelstahlrohr aufweisen. Die Güte der Beschichtung ist durch die von Güntner entwickelte Produktionstechnologie an jeder Stelle in der Tiefe des Blockes – auch in engsten Zwischenräumen – gewährleistet.
Der Güntner Coil Defender ist darüber hinaus auch für Produktionsumgebungen im hochsensiblen Lebensmittelbereich zugelassen, da die Pulverbeschichtung vom TÜV Süd als „HACCP-ready“ zertifiziert ist (HACCP = Hazard Analysis and Critical Control Points) (Bild 5).