Sichere Kälte- und Klimaanlagen: Druckabfall- und Druckanstiegsprüfung
Sichere Kälte- und Klimaanlagen: Druckabfall- und Druckanstiegsprüfung
Die Anforderungen an die Dichtheit von Kälte- und Klimaanlagen sind hoch. Einerseits, um ihre Funktionstüchtigkeit im Betrieb zu gewährleisten. Schließlich verursacht der Ausfall von Klima- und Kältetechnik in der Regel Kosten, die über die Reparaturaufwände weit hinausgehen – beispielsweise durch die Beschädigung von Maschinen aufgrund mangelnder Kühlung oder den Verderb von Lebensmitteln. Andererseits ist die Dichtheit der Anlagen grundlegend, um ein Austreten umwelt- und klimaschädlicher Kältemittel in die Umwelt zu verhindern.
Vorgaben der F-Gase-Verordnung
Die F-Gase-Verordnung, die 2015 in Kraft getreten ist, hat die Dichtheitsanforderungen sukzessive immer weiter verschärft. Eine zuverlässige Dichtheitsprüfung ist daher unabdingbar, um die Vorgaben des Gesetzgebers zu erfüllen. Hier sind nicht nur die Hersteller von Klima- und Kältetechnik in der Pflicht, sondern ebenso die Betreiber.
Ziel der EU-Verordnung EU-VO 517/2014 ist die schrittweise, signifikante Reduzierung der Treibhausgasemissionen, insbesondere der fluorierten Treibhausgase (F-Gase). Sie gilt sowohl für Kälte- und Brandschutzanlagen als auch für Kühlschränke und Wärmepumpen. Um diese Ziele zu erreichen, sind in der VO mehrere Instrumente vorgesehen, wozu auch die Erweiterung der Dichtheitsanforderungen und Zertifizierungen von Unternehmen und Personal zählen. Seit 2020 gibt es zudem ein Nachfüllverbot für bestimmte Kältemittel für bestehende Anlagen.
Zu den geänderten Dichtheitsanforderungen gehören Bemessungsgrenzen für die Füllmengen und Dichtheitskontrollen inklusive Aufzeichnungspflicht. Die Prüfintervalle sind vorgeschrieben und variieren je nach Kältemittel und Füllmenge. Ab einer Füllmenge von 500 t CO2-Äquivalent wird zudem der Einsatz eines Leckage-Erkennungssystems obligatorisch, das selbst auch regelmäßig zu überprüfen ist. Betreibern von F-Gase-Anlagen obliegt es zudem, Leckagen unverzüglich zu reparieren und innerhalb einer Frist durch eine zertifizierte Fachkraft überprüfen zu lassen.
Dichtheitsanforderungen für kältemittelführende Komponenten
In der Regel darf der Kältemittelverlust pro Jahr nur wenige Gramm betragen. Zusätzlich zur Umweltgesetzgebung kommen zumeist noch die eigenen Qualitätsansprüche der Hersteller. Kühlkreisläufe mit nur kleiner Füllmenge erfordern logischerweise auch kleinere zulässige Leckageraten. Eine Leckagerate pro Jahr von 3 g Kältemittel beispielsweise entspricht je nach Art des Mittels einer Prüfgas-Leckagerate – ob Luft, Helium oder Formiergas – von etwa 3 x 10-5 mbar x l/s. Angesichts derart hoher Genauigkeitsprüfungen ist es notwendig, gängige Prüfmethoden auf den Prüfstand zu stellen.
Druckabfallprüfung: Nachweisgrenzen werden nicht erreicht
Die Messung des Druckabfalls ist wohl die am häufigsten anzutreffende Prüfmethode. Das liegt vermutlich daran, dass sie einfach und schnell durchzuführen scheint und keiner großen Investitionen bedarf. Oft wird hierzu einfach ein analoges Manometer an den zu prüfenden Kältekreis angeschlossen.
Die Nachweisgrenzen der Methode liegen im besten Fall bei zirka 5 x 10-2 bis max. 1 x 10-3 mbar x l/s. Damit ist die Druckabfallprüfmethode aber um den Faktor 100 zu ungenau für die Dichtheitsanforderung an einen Kältekreis. Nötig wäre vielmehr eine Dichtheitsprüfung gegen Grenzleckraten in einer Größenordnung von 10-5 mbar x l/s.
Probleme mit der Ablesegenauigkeit
Die gängigen analogen Manometer haben meist eine große Skalierung bis 20 bar. Der kleinste ablesbare Druckabfall von einer Zeigerbreite liegt dann im Bereich von etwa 50 mbar. Ein Druckabfall in dieser Größenordnung tritt zum Beispiel in der Zeit von einer Stunde für ein System mit 2 l Füllvolumen auf, wenn die Leckagerate 2,8 x 10-2 mbar x l/s beträgt. Zur Erinnerung: Die für Kältemittel zulässige Leckagerate liegt im Bereich von 10-5 mbar x l/s. Das heißt, dass der Druckabfall, den man gerade noch ablesen kann, bereits um den Faktor 1 000 größer ist als die Grenzleckrate, gegen die man eigentlich prüfen müsste.
Temperatur und Druck beeinflussen sich gegenseitig
Eine Temperaturänderung während der Messung führt überdies zu einem verfälschten Messergebnis, da zwischen beiden Parametern ein proportionaler Zusammenhang besteht. Hierzu muss man das Prinzip der Druckabfallprüfung betrachten: Der Prüfling ist bis zu einem definierten Überdruck mit Prüfgas gefüllt, das durch vorhandene Lecks entweicht, wodurch der Druck sinkt. Wenn sich jedoch während dieser Messung der Druck infolge eines Temperaturanstiegs erhöht, werden eventuelle Leckagen einfach übersehen.
Lesen Sie auch:
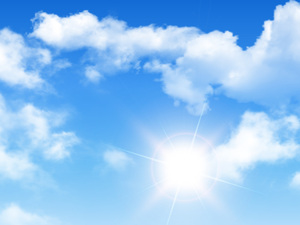
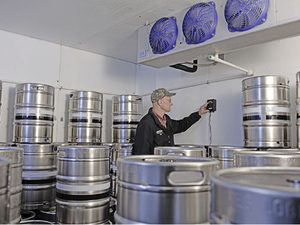
Diese Abhängigkeit des gemessenen Drucks von der Temperatur ist bei Prüfungen von Kälte- und Klimaanlagen besonders kritisch, denn einerseits beinhalten diese oft Wärmeübertrager, die durch ihre große Oberfläche den Druck bereits bei kleinsten Temperaturschwankungen beeinflussen. Andererseits haben Kältekreise in der Regel einen Betriebsdruck von 3 bis > 15 bar. Um praxisrelevante Testergebnisse zu erhalten, muss auch der Prüfdruck in diesem Bereich liegen. Befüllt man nun den Kältekreis mit dem Prüfgas, dann führt die Druckerhöhung von 15 bar und mehr dazu, dass sich der Kältekreis deutlich erwärmt. Während der Messung kühlt er dann kontinuierlich wieder ab. Eine störende Temperaturschwankung ist somit unvermeidbar. Die Folge sind endlos lange Stabilisierungszeiten.
Somit ist die Druckabfallprüfung doppelt ungeeignet: Neben der unzureichenden Genauigkeit erfordert sie auch noch viel Zeit. Überdies ist eine Lokalisierung des Lecks nicht möglich.
Druckanstiegsprüfung: Prüfdruck ist zu gering
Auch die Druckanstiegsmethode kommt bei gängigen Kältemittel-Füllanlagen häufig zur Anwendung. Das liegt vor allem daran, dass im System, um es zu befüllen, vorab immer Vakuum erzeugt wird. Nimmt man nach der Evakuierung und vor der Befüllung die Dichtheitsprüfung vor, lässt sich ein Arbeitsschritt einsparen.
Bei der Druckanstiegsmethode wird also zunächst das Prüfteil evakuiert. Steigt der Druck im System dann innerhalb der definierten Messzeit an, so ist dies auf vorhandene Leckagen zurückzuführen. Aufgrund des Vakuums sind Temperaturschwankungen für diese Prüfmethode weniger relevant.
Allerdings kann der Druckunterschied bei dieser Prüfung nur maximal 1 bar betragen, nämlich die Differenz zwischen dem atmosphärischen Druck der Umgebung und dem Vakuum in Inneren des Prüfteils. Relevante Leckagen, die erst bei Betriebsdruck von gleich oder größer 15 bar auftreten, kann man mit diesem Druckunterschied von einem bar kaum finden.
Keine einsatztypischen Prüfbedingungen
Komponenten und Bauteile in der Kälte- und Klimatechnik sind unter Betriebsbedingungen in der Regel mit Überdruck beaufschlagt. Die Druckanstiegsmethode findet jedoch unter Unterdruck statt, also genau genommen in falscher Druckrichtung. Laut DIN 1779 Punkt 8.4.2 soll die Prüfrichtung jedoch möglichst den Betriebsbedingungen entsprechen.
Auch die Druckanstiegsmessung ist daher ungeeignet, um die Dichtheitsanforderungen der Kälte- und Klimaindustrie abzudecken. Sie stellt, ebenso wie die Druckabfallprüfung, höchstens eine günstige Möglichkeit zur Grobleckkontrolle dar. Daher sollte sie allenfalls eine Ergänzung zu anderen, genaueren Prüfmethoden sein.
Dieser Beitrag von Autor Volker Trieb ist zuerst erschienen in Die KÄLTE + KLIMATECHNIK 01/2020. Volker Trieb ist Market Manager RAC bei der Inficon GmbH, Köln.
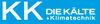
Dieser Artikel ist zuerst in KK DIE KÄLTE + Klimatechnik erschienen. Mehr Informationen erhalten Sie im kostenlosen Newsletter der KK.
Zur Anmeldung geht es hier.